Air hoses consist of lengths of industrial strength tubing that are used to transfer power or pressurised air from the compressor end to the tool's operation end. They are typically made from rubber and can withstand high pressures. They can be used for many different applications.
The manufacturing process for air hoses involves extrusion, spiral wrapping and calendaring. Then, they are placed onto shaped metal mandrels before being vulcanised with hot steam.
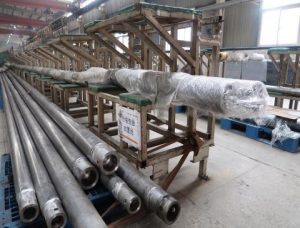
Air hose: pros and cons
Air hoses are lengths of industrial-strength tubing that transfer pressurised air from a compressor to the operating end of a tool. They can be used for a variety of applications, including spray painting, welding and carpentry. They can also be used to power pneumatic nozzles and tools, such as staplers and jackhammers. The hose's strength and flexibility will depend on the application. Air hoses are available in many different lengths and materials. Air hoses are available in a variety of lengths and materials.
The maximum pressure rating of an air hose defines how much force can be exerted on the hose during operation. This is a safety feature to prevent the hose from breaking under excessive pressure. The maximum pressure rating of a hose is determined by its material and internal design. For example, a hose made from rubber is more resistant to high pressures than a hose made of PVC.
The hose must also be able withstand the chemical properties that any gasses are transporting. It must also be able resist environmental factors such as UV rays and cold temperatures. A hose must also be flexible, easy to store and handle. It should be flexible and not lose its flexibility with time.
ways to extend the life of air hoses
Air hose lifespan is affected by many factors, including operating conditions, environmental conditions, as well as a proper maintenance schedule. Hoses should be inspected regularly for damage, kinks, and twists. They should also be properly coiled on the reel to avoid unnecessary stress on the rubber hoses. Air hoses can be extended by using elbows, adapters, and maintaining the correct hose length.
It is important to keep in mind that different tools require different air flow ratings. Some tools, like handheld nailers, need low CFMs, while others, like portable compressors, need higher CFMs. Hoses with larger bore diameters are required for the latter. A careful hose selection will increase the value of your system.
Some hoses are limited in their shelf life, acceptance and service. This is usually 12 years after the cure date for bulk hoses or hose assemblies. This lifespan includes a period of time from the acceptance and receipt by the customer until installation into service. It is recommended that all hoses and hose assemblies be protected from fuels, oils and solvents while in storage. In addition, hoses should be stored in an area where they will not be exposed to direct sunlight or heat sources.
air hose wire layer fault
Air hose wire layer fault is a condition that occurs when the internal pressure of the hose changes significantly, causing the steel wires to rub against each other. The wires break and the hose fails. This issue can be caused by a variety of factors, such as excessive system pressures, kinks in the hose, or cover damage that exposes the reinforcement. It is important to inspect the hose assembly regularly, and to ensure that it is properly rated for your application.
Another common problem with hoses is over bending them. This can be due to improper installation, mishandling during transport or shipping, or by using a hose that is rated for a higher working temperature than your application requires. Over bending your hose can lead to a loss in the working pressure, restricting the flow of media through the assembly, and increasing heat-buildup within the hose and surrounding equipment. If you over bend your hoses they may start to vibrate or whip uncontrollably. In this case, it is best to replace the hose with one that is rated for your system and has the proper working temperature. It is helpful to add a whip-inhibiting mechanism at the coupling.