Bop Control Hose
release date:2023-08-14 09:41:13
reading volume:
share:
The bop control hose is a hydraulic line that is used to operate the blowout preventer (BOP) system. The hose must be able to maintain operating pressure and stand up to fire and high heat conditions. The coiled tubing Quad BOP typically has Pipe and Shear ram assemblies with Contingency and Wireline rams as well. These Combi rams provide increased flexibility and reduce the amount of stick-up compared to a conventional quad BOP.
Types
There are several types of bop control hose for use in BOP (blowout preventer) equipment stacks. They supply hydraulic operating fluid to a series of functions located on the top of the stack, including shear rams and blind shear rams. These rams are designed to shear a pipe or seal a well bore, respectively. The shear rams have steel blades that are able to cut through the drill pipe and seal the annulus when activated. The ram-type BOP has rubber faced, steel rams that come together with immense force to seal the well bore. It is typically positioned above the quadruple or twin ram BOP in a coiled tubing, workover, or stripper-packer stack. The ram-type BOP also has a choke manifold that redirects mud into the BOP during a kick, and a kill line valve to direct coiled tubing into the BOP during shear ram activation. BOPs require a large volume of hydraulic operating fluid stored under high pressure in the accumulator unit. Bundled hoses exhibit greater volumetric expansion when pressurized than identical hoses in isolation. This increases response times for the pod-mounted relay valves when activated by a hydraulic pilot signal.Applications
Blowout preventer (BOP) systems are a critical safety measure to protect the well during a drilling or production event. Despite the robustness of the overall system, control tubing, hoses and fittings can be vulnerable to failure.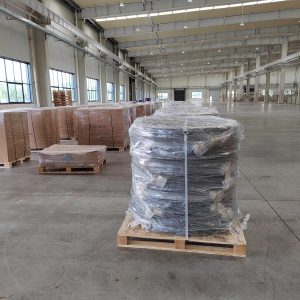