API BOP Hose
release date:2023-08-14 09:45:16
reading volume:
share:
API BOP Hose is made with high quality components to operate under harsh crisis oil field conditions. It is designed to maintain its required operating pressure in the event of severe fire exposure. This type of BOP control hydraulic hose is specified by API 16D, suitable for high pressure hydraulic applications on drilling control equipment and capable of containing its rated operating pressure in flame temperatures up to 1300degF(700degC) for 5 minutes.
High Pressure
BOPs are designed to contain the erratic pressure (known as a formation kick) and uncontrolled flow of oil, gas and drilling fluid that occur when drilling a well. These systems control the pressure of the drilled hole and prevent tubing, drill pipe, tools and the drilling mud from being blown out of the well, which is known as a blowout. API 16D BOP control hoses are manufactured with superior components to operate under tough crisis oil field conditions. These hoses are capable of maintaining their rated working pressure in the harshest fire exposure environment for a minimum of five minutes. Rig operators must submit accumulator precharge pressures for District Manager approval prior to BOP stack deployment and calibration to OEM specifications. However, this requirement would be burdensome for most equipment owners. Chamber pressure tests are already required at a minimum of yearly, and when equipment is repaired or remanufactured. Using these tests to determine accumulator precharge pressures would be more efficient and cost-effective.High Temperature
BOP control hoses are manufactured with superior components that allow them to operate withstand tough crisis oilfield conditions such as high temperature and fire exposure. These hoses are designed to hold full working pressure and allow the system to continue operations even in the most severe fires. Blow-out prevention (BOP) systems are a vital part of the overall safety and operational capability of oil drilling rigs. The system is responsible for sealing the well in case of a blowout. This is accomplished with a combination of mechanical and hydraulic control devices that can be activated when primary well control fails or when the situation calls for emergency well control measures.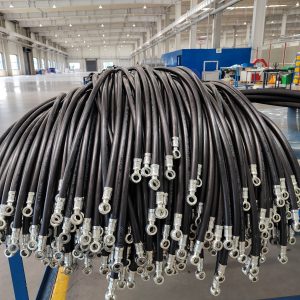