Blowout preventer (BOP) systems provide fail-safes for drilling operations. Having a system in perfect working order is vital for the safety of personnel, equipment and the environment.
The control hoses used in these systems are required to withstand high pressure, heat and flame exposure. Gates BlackGold MegaShield 5000 is the perfect solution to these demanding requirements.
Flame Resistant
Fire resistant means the hose is designed to keep its working pressure in a fire situation. This is very important for BOP systems because it can keep the pressure in place and allow the rest of the system to continue operating in case of an emergency.
BOP hydraulic control line hoses (API 16D) used on blow-out preventer systems are manufactured with superior components to operate withstand tough crisis oilfield conditions including fire. They are capable of containing the hose rated working pressure in a flame temperature of 1300 degF (+700 degC) for 5 minutes.
They are made of multiple layers of textile fabric and steel cable with one layer middle rubber placed between the cable layers and a stainless steel armored cover to handle abrasion, corrosion, cutting, gouging, oil and weather. They also feature crimped couplings that can withstand high temperatures and abrasion. BOP hoses are available in various sizes and working pressures. These are also offered in a range of end configurations like NPT, JIC and BSPT.
Corrosion Resistant
The ability to withstand corrosion is an important feature of any metal hose. Many of the alloys used in flexible metal hoses, such as Monel 400 and Hastelloy C-276, have excellent resistance to media. The wall thickness of a hose also impacts its corrosion resistance, with thicker walls having higher levels of protection from harsh environments and media.
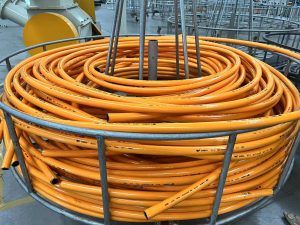
Blowout preventer hoses are used to connect the BOP and other equipment on drilling platforms. They must be able to withstand high pressure and fire exposure. Our BOP control lines meet API 16D standards and can withstand a minimum of 1300 degF (+700 degC) flame temperature at rated working pressure for five minutes.
Abrasion Resistant
In industrial applications that involve equipment with over-the-sheave hose assemblies, abrasion damage can cause costly downtime. Parker offers abrasion resistant solutions such as protective shields and covers that are compatible with most hose types and work environments.
BOP hose is the main line that connects the blowout preventer to the choke manifold and kill valvs for well control operations. This hose is designed to withstand fire exposure at 5, 000 psi for 5 minutes.
For more targeted abrasion protection, Parker’s NEXWRAP chafe guard and ParKoil polymer spiral wrap can be used to bundle hose, tubing and wires and protect them from harsh environments. These wraps can be installed without shutting down equipment first, preventing unnecessary downtime. For other abrasion resistant protection, Parker’s spring and armor guards are ideal for boom and cable track applications. These guards prevent hoses from pulling out of fittings during repeated cycles of friction.
Heat Resistant
Designed for hydraulic use and certified to withstand fire, high heat and pressures in safety critical applications. This armored hose meets API 16D flame test requirements of 1300°F at working pressure for five minutes.
Unlike conventional BOPs, the single pair of opposed rams of this invention achieve both mechanical and hydraulic seals with the wireline. This is achieved because the rams when closed cooperate to form a small centralized grease sealing chamber of relatively small dimension which is injected with grease under high pressure to establish protective hydraulic sealing between the elastomeric rams and the BOP body structure.
The system incorporates a pressure equalization valve assembly which is utilized to reduce friction between the rams and the body structure of the BOP when the rams are opened. This effectively minimizes the force that must be applied to open the rams and reduces signal time to operate the BOP. This helps to prevent accidental blowouts. In addition, it reduces the volume of subsea fluid storage accumulators required since the usable accumulator capacity diminishes with increasing water depth.